Introduction
Over the past few decades, 3D printing technology has become increasingly accessible with the advancement in computer and software development. The potential that this new way of manufacturing brings to the gaming industry is remarkable. 3D Printing technology provides a unique solution for gamers wanting to make their own customized miniatures and pieces for board games.
Using a CAD software program, it’s possible to design the exact shape, colour, size and other features desired; by changing a few parameters in the software you can easily create hundreds of different variants without having to order large batches of physical parts or wasting materials during mass production. In addition, 3D printing also opens up possibilities for creating entirely new gaming pieces using more intricate designs than previously achievable – allowing you to explore your creativity in ways not possible before. Furthermore, because 3D printing does not require a physical mold as other traditional methods do, it makes custom miniature production an affordable novel way for game enthusiasts to show off their unique creations and give them an edge over the competition.
Benefits of 3D Printing
3D printing board game miniatures has a range of benefits for players. Firstly, it is cost effective as there are a range of materials available at relatively low costs. For example, PLA plastic filament which is suitable for home 3D printing is one of the most commonly used and affordable options. The cost of 3D printing miniatures also decreases when larger batches are printed. Secondly, due to advancements in the quality of 3D printers, the end product can be highly detailed and accurate to design specifications. Players that want to customize their models can easily add elements in CAD software and they can be printed within hours. Finally, 3D printing makes it incredibly convenient as builds can take place within the comforts of your own home and with minimal setup time required.
Finding Popular 3D Models
For gamers interested in 3D printing their own board game miniatures, there are a variety of excellent resources available for locating great 3D models. A good starting point begins with searching popular websites and forums dedicated to 3D printing.
One of the most popular sources for finding high-quality 3D models is the website Thingiverse. It provides an extensive library of free public domain STL files, including various types exciting board game miniatures created by the community’s members. Many of these 3D models contain detailed instructions on how they were generated.
Additionally, popular forums like Reddit, Facebook groups, and other social media platforms focus exclusively on various topics related to 3D printing. They provide invaluable tips and advice on creating your own unique board game miniatures and suggestions on how to print them successfully. Not only that, but these forums also offer a wide range of pre-made 3D models from helpful users who have graciously shared their work with others in the community.
Online marketplaces like Shapeways are another great option for those looking for professionally designed 3D models specifically made for board games. These marketplaces include offerings such as licensed characters from RPG games, miniature terrain pieces, themed objects like dice towers or tokens”all designed by experienced creators who specialize in this field. The downside is that these designs can be expensive when compared to downloading a few STL files from established websites or freely from social media platforms mentioned above.
Preparing the Files
When preparing 3D files for printing board game miniatures, it is important to ensure that the files meet certain requirements in terms of software and settings. The type of software used will depend on the desired level of quality and detail. Popular choices are CAD (Computer-Aided Design) programs such as Solidworks, TinkerCAD, or SketchUp. No matter the program of choice, it is vital to setup prints with an appropriate ‘slicer’, which converts a 3D model into instructions for a printer. The slicer divides the model into layers, allowing for modification of important variables such as infill percentage and support structures for parts overhanging in mid-air. Finally, it is important to check the bed leveling of printers prior to beginning a print job – this helps eliminate warps that can occur from uneven heating between different areas within a print bed. With all these steps taken care of, you’ll be ready to start creating detailed board game miniatures.
Different Types of 3D Printers
FDM (Fused Deposition Modeling) 3D Printers:
FDM 3D printers use filaments to create a 3D object by melting, extruding and depositing material layer-by-layer. This type of printer is relatively inexpensive, as it uses common thermoplastics like ABS or PLA filament, which is then melted and carefully constructed. The FDM 3D printing methodology is fairly straightforward for board game miniatures – making it accessible for people with limited experience creating complex objects in three dimensions.
SLA (Stereolithography Apparatus) 3D Printers:
SLA 3D printers employ photosensitive resin that hardens upon exposure to ultraviolet light. These machines use an ultraviolet laser beam to trace the shape of an object onto a thin vat of liquid resin, hardening its surface layer while leaving behind unexposed liquid material at its bottom. SLA prints are typically more detailed than FDM prints and require less finishing work to prepare them for use in your favorite games. However, this method is usually more expensive due to the higher costs associated with UV resins.
SLS (Selective Laser Sintering) 3D Printers:
SLS 3D printers use a high-powered laser beam to selectively fuse together powdered materials such as metal alloys or polyamide into solid shapes based on digital designs. This is often used for dry powder metals including aluminum, stainless steel and titanium but polyamide resins are available as well allowing the creation of tough nylon parts requiring less finishing compared other techniques making it the preferred choice when producing detailed figures such as custom game pieces and components. As this method requires equipment with a greater level of sophistication and skill to operate correctly, it usually has higher costs associated with it when using outside services
Filaments and Materials
When it comes to 3d printing board game miniatures, selecting the right filament and material is key. Each type of material has its unique advantages and disadvantages that must be taken into consideration. The most popular filaments used for 3D printing board game miniatures include PLA (polylactic acid) and ABS (Acrylonitrile Butadiene Styrene). Both offer great strength, durability, flexibility, and affordability.
PLA is the more popular option between the two due to its ease of use and biodegradable properties. It is manufactured from renewable resources such as sugarcane or cornstarch which makes it eco-friendly. Its low melting point makes it easy to work with on 3D printers since no heated bed is required but prints can tend to be relatively brittle. PLA also has a glossy finish due to its light colored nature making it ideal for projects where aesthetics are important.
ABS on the other hand requires a heated bed due to its higher melting point but it comes with much improved strength compared to PLA with better impact resistance making it great for parts that need extra durability or flexibility such as gears and mechanisms. Its matte finish gives a more realistic appearance than PLA’s glossy finish making it well suited for painting afterwards. It is however not as widely used as PLA because of its poor environmental record and hazardous emissions associated with its manufacturing process so best avoided if sustainability matters for your project.
Design Considerations
Sizing: It is important to consider the size of the mini when a design is being produced. Most miniatures that are designed for board games are between 25mm and 35mm in size. It is important to ensure that the model is scaled properly before printing so that it fits properly with other miniatures during game play.
Shapes: When designing 3D printed miniatures for board games, one should consider appropriate shapes and proportions. Often, minis should have proportionally balanced shapes with smooth curves and lines. Incorporating multiple angles into the design creates visual interest while also helping players differentiate them from other pieces during game play.
Features: To make 3D printed board game miniature designs look more attractive and realistic, one could add various intricate details like facial expressions or weapons on figures, or furniture and décor items into non-human characters designs. Embossing or debossing fine details such as patterns onto minis can also be used to further enrich their appearance. Additionally, textures applied on surfaces can help make them appear lifelike as well.
Post-Processing Steps
Sanding: After 3D printing, your board game miniature may have some rough edges and prints lines. To make it look smoother, sanding can be done to remove those lines and edges. To achieve a good result use the right grit of sandpaper. Depending on the size and detail of the object, you may need to do sand with more than one grit of paper (for example, 120 first, then 400). Make sure you don’t forget to sand any internal corners or crevices for a uniform finish.
Painting: Once you have completed the sanding process, now it’s time to give your model a unique finish through painting. Start by applying primer, which will allow the paint to stick properly to the surface of your model instead of coming off soon after application. Then choose the colors that best represent your design/style and start with light coats so that all sides is evenly covered with paint and no details are missed out. Finishing off with a few more layers depending on how much coverage you desire.
Finishing: To give your board game figure an extra bit of realism and highlight any existing facial features or add glossiness to different areas of the miniature using varnishes such as spray or brush-on sealers will help protect all steps taken thus far from damage or from wearing off easily over time as well as making sure your mini is ready for years ahead in gaming sessions!
Final Thoughts
3D printing board game miniatures is an exciting way to add a personal touch to one’s gaming experience! This technology allows you to customize the look, scale, and design of your miniature pieces in whatever way you want. 3D printing also lets people take part in all aspects of the design process, giving them far more control over how their miniatures look compared to other traditional production methods. Not only can you customize the design of your pieces, but it will also save time and money due to decreased labor costs. Furthermore, 3D printing allows for faster prototyping of pieces as it eliminates many steps in the manufacturing process. All-in-all 3D printing offers gamers around the world an unparalleled level of detail and customization when designing their own figures that would otherwise be impossible with traditional methods.
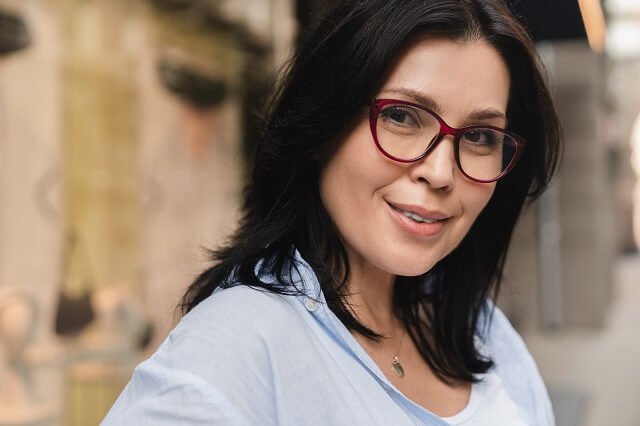
I love playing all kinds of games – from classics like Monopoly to modern favourites like Ticket to Ride.
I created this blog as a way to share my love of board games with others, and provide information on the latest releases and news in the industry.