Introduction
The board game manufacturing process is one of creative creation, design, testing and innovation. It requires the development of the game concept, the game mechanics, artwork and components for the game like dice, cards or figurines.
The cost to manufacture a board game can vary greatly depending on certain factors including how many copies are produced, where they are made, who manufactures them, and of course the cost of materials used. The goal is to find an optimal balance between minimizing production cost, meeting quality standards for the final product and making sure that all deadlines are met in order to make the process successful. Additionally there are other costs to consider when manufacturing a board game such as marketing costs, prototyping fees and analysis fees.
Creating a successful board game involves various tasks ranging from hiring a talented artist or graphic designer to create attractive visuals as well as researching which types of components will be necessary in order to ensure playability and entertainment value. Through this process developers must often also pay consideration to safety regulations in order to ensure that their games can be sold legally and rated appropriately amongst consumers.
Lastly manufacturers must identify appropriate strategies for distribution such as through traditional methods such as local resellers or ecommerce sites where games can be easily listed for consumers in the area. Whatever strategy selected it’s important for developers to plan out enough lead time so that their products arrive at stores when desired by customers.
In summation creating a successful board game is an exciting but costly venture since there are numerous facets involved along with various challenges throughout each phase of the manufacturing process ranging from designs phase to pre-production all while adhering to strict budgets along with industry regulations in order produce viable products within desired timelines alongside meeting quality standards demanded by consumers that engage together through shared gaming experiences!
Types of Materials Needed
The cost of manufacturing a board game depends on a few factors, such as the materials used, how many units are being made, and what type of services are needed. To help determine the cost, let’s take a step back and evaluate the components that make up a board game.
Most board games require a combination of cardboard or wooden pieces, plastic tokens, dice or cubes, and various artwork elements such as printed cards or boards. Depending on the design of the game some of these components can be replaced with electronic parts such as sound chips or electronic lights. The complexity and scale of these components should be considered when coming up with an estimate for manufacturing costs.
In addition to accounting for all the different pieces that make up the board game, other services may be required for production. This includes processes such as die-cutting and lamination of cards and boards, assembly of complicated mechanisms like metal spinners, testing game structures in sets with multiple players to ensure proper performance before mass production takes place. Professional artists may also be commissioned to create unique artwork for boxes, packaging and other gaming accessories that come with the board game. All this needs to be taken into consideration when pricing out product manufacturing costs.
Cost of Materials
The cost of manufacturing a board game will vary greatly depending on the complexity of the design and quality materials used. Board games usually consist of physical components such as cards, tiles, boards etc., which all need to be sourced and produced. Depending on the game, these components can range from being very basic to highly complex, thereby significantly increasing the cost of production. The higher the component quality is, the more it will cost in terms of materials that must also be sourced. This can include plastic pieces with molded shapes, printed artwork components or detailed figurines as well as metal coins and other token pieces for tracking score or progress in a game. If artwork or special images must be created for cards or boards then specialized printing may also add costs for texturing or unique color palettes. Additionally, any embedded electronics such as audio sound effects or sensors embedded in cards and tokens can give a modern depth to a classic game but this too adds complexity and bumps up costs associated with manufacture.
Tooling & Packaging Costs
A crucial element of production cost for any board game is associated with making smart choices on the tooling and packaging material. When creating the components, boards, tokens and pieces necessary for each game, manufacturers have to carefully consider what types of machines they will use to produce the final product as well as which type of packaging material is best. There are different costs associated with each choice and this impacts the total manufacturing price point.
The type of machine chosen to mass-produce the components of a board game can vary significantly in terms of cost. The time it takes to fabricate these parts is an important factor when choosing which machines are most suitable however the cost can be driven down if other methods such as moulding or die-cutting are used. If a manufacturer chooses not to outsource production completely, then choosing machines appropriate for game’s specific needs is essential. Purchasing a machine with multiple uses saves money in comparison to outsourcing certain processes where each individual task costs more than buying one all-inclusive machine.
In addition to tools and machinery, packaging must also be considered when considering how much does it cost to manufacture a board game. Cardboard boxes that require glue or taping can sometimes work out to be cheaper than plastic boxes, but those might not provide enough protection for components during transit and can be difficult to assemble manually due to lack of pre-made folds or predefined shapes. It could turn out being more expensive long term than an initial expenditure on a harder durable sturdy plastic box along with custom inserts that help hold pieces securely in place; but again this depends on individual context and may vary depending on complexity level required by our client’s desired end product.
Production Volume
The cost to manufacture a board game can vary greatly based on factors like production volume and quality of components. For example, when manufacturing a board game in low volumes, the cost of each unit can be relatively high due to the additional costs associated with manual assembly. On the other hand, increased production volumes require larger investments in machinery, tooling and manufacturing processes which may bring economies of scale but also comes with higher initial setup costs. Therefore, businesses must balance these considerations to pick the best option for their budget and needs.
In addition, more complex board games may require higher quality components such as plastic pieces and cards. The cost of these components are often driven by their complexity ” more intricate designs will usually come at a higher cost to manufacture than simple pieces. By assessing the type and volume of required components, businesses can set realistic expectations regarding their production costs and ensure that they are able to produce good-quality products within their desired price range.
Design & Artwork
The cost of designing and creating a board game’s artwork can vary significantly depending on the complexity. Simple artwork featuring cartoon-like illustrations only require one or two artists to provide able work, while intricate games with multiple components may need an artist to handle artwork for each component. The overall cost of artwork will be determined by factors like how many components are involved, how detailed they are, and how long it takes to produce the materials. Some boards may require prototypes and revisions, adding additional costs as well. Additional factors include the use of color and printing options such as embossing or spot varnish. Depending on the desired result and project scope, engaging a graphic designer may also be necessary to create art assets that bring your vision to life.
Variable Costs
Creating a board game typically involves a variety of variable costs. These include the cost of materials, such as cardboard and plastic pieces, the fees to obtain licenses for using any copyrighted material (if licensable content is included in the game design), and the cost of any marketing or promotional materials associated with launching the product. Additionally, depending on the manufacturer chosen for obtaining printed parts and packaging, there may be tooling costs associated with creating dies or molds and non-recurring engineering charges due to changes that need to be made along each step of the production process.
The good news is that it is possible to take steps to minimize unforeseen costs, such as being meticulous in design planning when working with an external manufacturer and taking advantage of economies of scale by ordering large quantities of components. Additionally, some manufacturers offer discounts if purchased components are used more than one time in their products; this should also be taken into consideration when making calculations during game design. Finally, rather than purchasing all components separately, many board game producers find benefit in ordering complete manufacturing kits from sources like Panda Manufacturing who can provide all necessary components at a set price per unit.
Total Costs
The costs of creating a board game can vary greatly, depending on the individual goals associated with the project. Factors such as game complexity, quality of art materials, manufacturer chosen, and game marketing budget will all have an impact on overall prices.
The first step in budgeting for a complete and high-quality board game is to develop a cost estimate. Some of the initial expenses to consider include: artwork design, concept and graphic consultation such as hiring an artist to create illustrations; creating and sourcing components such as dice, cards, tokens, boards etc; advertising & marketing; copyright/trademark application fees; tooling costs for producing molds for plastic parts; professional video and photography services for promotional purposes if needed; shipping costs both domestically and internationally prior to sales launch.
Once these expenses are tallied up it’s important to account for royalties or licensing fees which could be paid over the course of several years if you decide to go down that route. After this not-so-small list is established it’s then essential to factor in some type of cushion funds in case anything goes wrong along the way. This will prevent any unpleasant surprises when unexpected expenses pop up during production.
Depending on all of these factors involved in creating a board game an estimated total cost could range anywhere from $8K – 30K before any profits are made from sales. Generally speaking this kind of expense requires support from family or investors who share faith in your project or provide funds based on projected future earnings . Working together with professionals who are experienced in this kind of venture can also be beneficial as they bring expertise and guidance which may save time and give direction throughout different stages .
Exploring Alternatives
When it comes to manufacturing a board game, costs will vary greatly depending on the type, size and complexity of the game. It is important for manufacturers to explore their options in order to save money and maximize their budget. One way of doing this would be to create a prototype of the game before fully committing to production. This allows for problems or shortcomings to be identified early on, so that adjustments can be made rather than having chips reproduced multiple times or making costly changes after the fact.
Another way manufacturers may look at saving money is by looking into alternative materials such as cardboard over thick paper stock; creating game parts with minimal components; and working with fewer colors than originally planned, opting only for two or three colors instead of a more complicated palette. Manufacturers should also consider local versus offshore production facilities, taking into account minimum order quantities along with the cost of freight when making their decision. Furthermore, companies should recognize that bulk orders may come with stock discounts when producing large numbers. Finally, packaging and logistics often make up a larger portion of cost than raw material and labor expenses; selecting lighter packages with fewer components will help lower these costs.
Conclusion
The cost of manufacturing a board game largely depends on the type and complexity of the product, but there are some general expectations when it comes to cost. Generally, small run board game productions”less than 2,500 units”range from $10-$20 a unit for a basic game design with minimal artwork; however, additional features such as tin containers for storage or custom dice can drive up production costs.
Large runs of 10,000 units and up can start at $3-5 a unit depending on complexity, size, and materials. It should also be noted that whatever manufacturer you work with will likely require a minimum order; this ensures they can cover the costs associated with tooling and other related production set up costs.
In terms of charges outside of production, you’ll need to factor in shipping expenses between factories if parts are sourced internationally. Additionally, graphic design fees and packaging development will add to your bottom line; quality control checks have incremental cost considerations as well that must be taken into consideration. The IP rights register fee should not be overlooked either; registering the game design will help protect the product from being knocked off by unscrupulous distributors.
Manufacturing a board game carries immense potential benefits including long term revenue streams apart from traditional sales channels like kickstarter or marketplaces (especially if merchandise is sold). Extending out into digital versions down the road is attractive to many creators as well considering larger audience expansion potential. However, scaling production also has drawbacks due to selling obligations associated with distributors and retailers in certain regions which require large inventories and working capital investments on behalf of the producer that don’t always pay off initially depending on consumer response rates for the product.
There are numerous factors to take into account if you decide to manufacture a board game: cost per unit along with additional ancillary expenses related to set up such as art direction outreach /talent agency recruiting fees (if applicable) shipping costs etc., Protecting intellectual property rights through registration so knockoffs cannot occur easily while also following manufacturing regulations locally/internationally (depending on production fashion) To conclude: Until you have ample resources in place “configured funds ready access to local agencies who understand your development needs evaluation feedback regarding target markets investment research/scheduling aimed towards sustaining adequate inventory expected forecast manageability”manufacturing a board should be approached thoughtfully””researching key players associated with forming strategic partnerships—- It may prove difficult otherwise for entrepreneurs attempting large scale projects for board games””cost restrictions leading constraints legal liability fluctuations account upkeep etc.. “”but due diligence beforehand makes all parties involved more confident in succeeding!
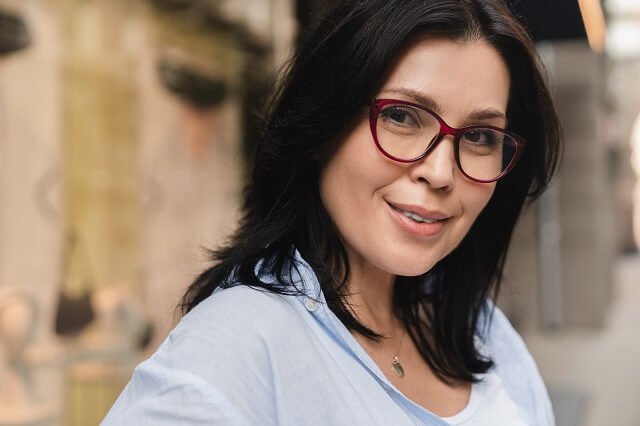
I love playing all kinds of games – from classics like Monopoly to modern favourites like Ticket to Ride.
I created this blog as a way to share my love of board games with others, and provide information on the latest releases and news in the industry.