Cost Analysis
3D printing for board games is a cost-effective way to produce quality products. The initial capital outlay for 3D printing technology is relatively low, however the infusion of new designs will require additional spending due to the costs associated with software licensing, individualized job programs, and raw materials. When factored in, the overall cost can become expensive depending on the complexity of the design project.
However, these costs are markedly lower compared to traditional manufacturing and assembly costs associated with producing services by hand. Customization and production from scratch typically require even more resources and time. While 3D printing does take a bit of time in terms of calibrating machines and setting up jobs, it tends to has significant cost savings for those willing to look into its advantages over traditional methods. Furthermore, when scaled up to mass production levels or used for prototypes that may lead to further customization down the road, 3d printing can be excellent value as it drastically reduces lead times coupled with massive savings on labour costs related to assembly sections of production that are required during traditional manufacturing methods. These savings should offer companies economic benefits in both tangible products and productivity.
Challenges of 3D Printing for Board Games
3D printing for board games can offer unique creative opportunities, but there are also many challenges to consider. One of the main issues is the time it takes to print a game board on a 3D printer; depending on the complexity of the design, this process can be incredibly labor-intensive and could take days or even weeks. Additionally, designing a complex two- or three-dimensional board game with shapes and objects that need to fit together in perfect symmetry can present its own difficulties. Finally, because 3D printing is relatively new technology and still largely experimental, there may be limitations to available materials and colors when creating more complex boards.
3D Printing Software
There are several types of 3D printing software that board game makers can use to create their designs. The three most common types of software are CAD (Computer-Aided Design), Mesh Repair and Vector Arts.
CAD is a computer design program used for creating objects in both two and three dimensions. It allows users to take a shape or model from a two-dimensional drawing and turn into a three-dimensional structure which can then be printed out with a 3D printer. With CAD, creators can also add text, details, and shapes to their designs, making it one of the more popular options for board game makers.
Mesh Repair is another type of 3D printing software that board game makers can use to bring their ideas to fruition. This type of software repairs any holes or problems found in object mesh files, making them ready for 3D printing. This type of software is best suited to those who are using existing models as it helps repair any mistakes found within the object files before they’re printed.
Finally, Vector Arts is often used with 3D software programs like CAD and Mesh Repair as an accompaniment to create more detailed designs for printing out with 3D printers. Vector Arts allow for an array of intricate shapes and patterns that may not be available under the other two programs. It an invaluable tool for designers looking for unique prints that stand out from all others!
When choosing which type of 3D printing software works best for you when making board games, consider factors such as your skill level, cost, features offered etc., Depending on your needs and how complicated your project is; one or more of these options may be suitable for you!
Intellectual Property
Board game makers should consider intellectual property rights when 3D printing their games. This includes having a strategy for trademark protection and copyright enforcement in place. Trademarking the title, artwork and other unique elements of the board game to prevent competitors from copying it is important. Additionally, having a copyright registration on any written material related to the board game is essential when considering 3D printing rights. It would be advised to secure a licensing agreement that grants permission for others to print your game in 3D which allows the licensee royalty payments for copies sold by them. Finally, makers should understand other countries’ laws related to protecting intellectual property and take necessary steps if needed.
Aftercare
Storing 3D printed board game pieces is an important part of ensuring lasting durability and enjoyment when playing. It is best to store these pieces in separate containers that are separated from one another so that they don’t rub together, potentially causing scratches or other damage. If it is necessary to place the pieces inside of a game box, make sure they are lined with something soft and gently place them back in the box after each use.
Maintaining 3D printed board game pieces is fairly straightforward since they should not need any regular upkeep. Just make sure that any liquids are wiped away and dried quickly if there is accidental spillage on the pieces to prevent staining or discoloration. Additionally, avoid exposing the pieces to direct sunlight for long periods of time as excessive UV exposure could cause fading.
If one of your 3D printed board game pieces becomes damaged, depending on how substantial the damage is you may be able to fix it yourself by sanding down and reshaping the piece or patching its surface with some filler material or paint. However, if it’s a serious issue such as electronic malfunctioning in some cases, then it might be best for you to seek out an expert for assistance.
Tips and Tricks
1. Design a board game that fits within the build parameters and physical limits of your 3D printer, ensuring you don’t get objects that are too large or too small.
2. Make sure all your designs are optimized for 3D printing to achieve an accurate and precise result ” this includes using appropriate wall thicknesses, print orientation and support structure.
3. When creating complex pieces or shapes, consider faster printing processes such as Fused Filament Fabrication (FFF) as they allow more intricate designs with detail-oriented layers.
4. Use slicer programs to adjust settings such as temperature, speed and filament type according to your model material and details required.
5. For intricate parts or games pieces with many interlocking elements, you may wish to consider printing at a lower resolution with long fast moves across the model material in between detailed structures for maximum accuracy over time saved.
6. Finally consider adding colour ” digitally or manually ” by painting the completed pieces for a truly polished design ready for play!
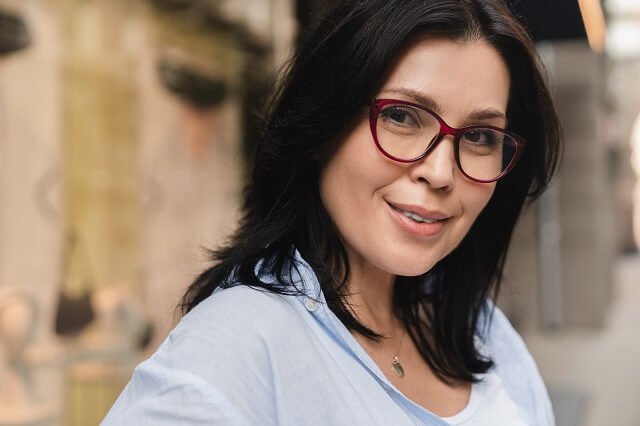
I love playing all kinds of games – from classics like Monopoly to modern favourites like Ticket to Ride.
I created this blog as a way to share my love of board games with others, and provide information on the latest releases and news in the industry.